Austenitic stainless steels
Austenitic stainless steel flat rolled products and strips
(EN 10088)
Austenitic steels are particular chromium-nickel alloys which feature chromium contents varying from 16 to 26% and nickel contents from 6 to 22% besides generally having a very low carbon content, below 0.1%.
Austenitic steels are insensitive to brittle fracture and useful for low-temperature uses.
Stainless steels can be easily welded to other stainless steels and to common carbon steels.TIG welding processes, plasma arc welding, MIG and resistance welding are all particularly suitable for stainless steel.
Excellent processability especially for cold deformations and machine tools.
Uses
Food, chemical, pharmaceutical, paper, naval and aeronautic industries; excellent for welded appliances of even considerable thickness; also for furnaces, boilers and burners.
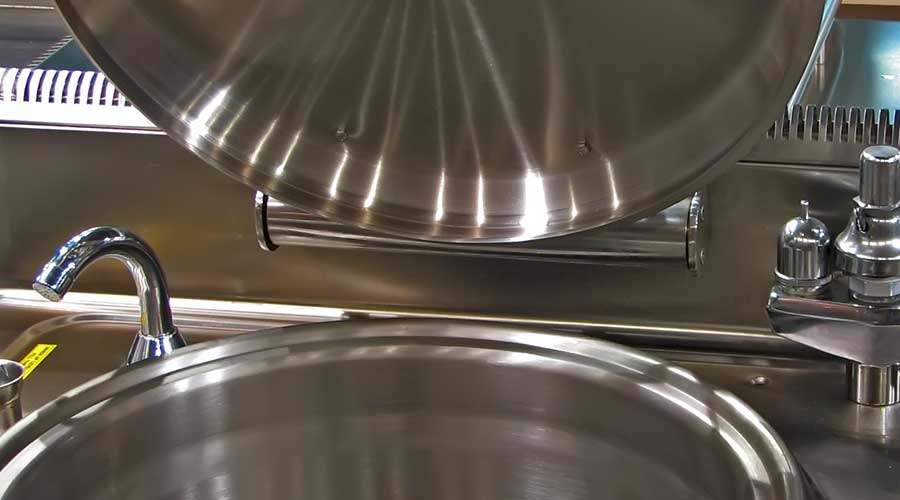
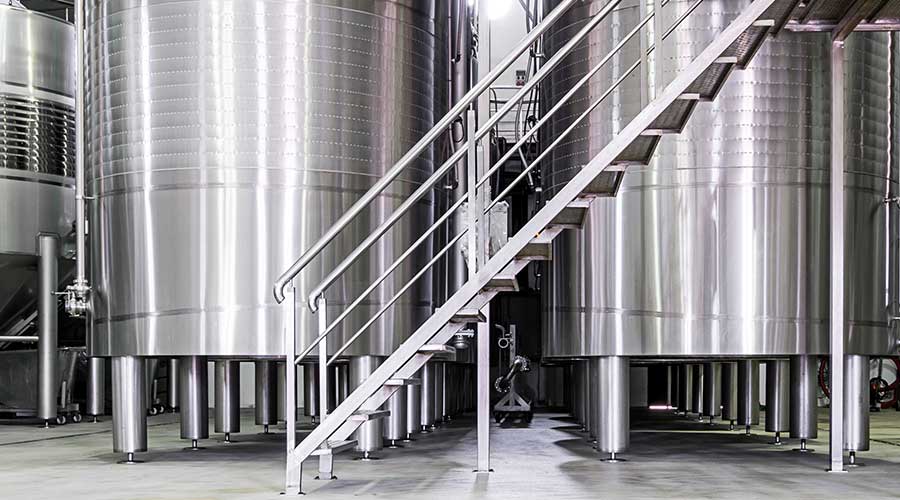
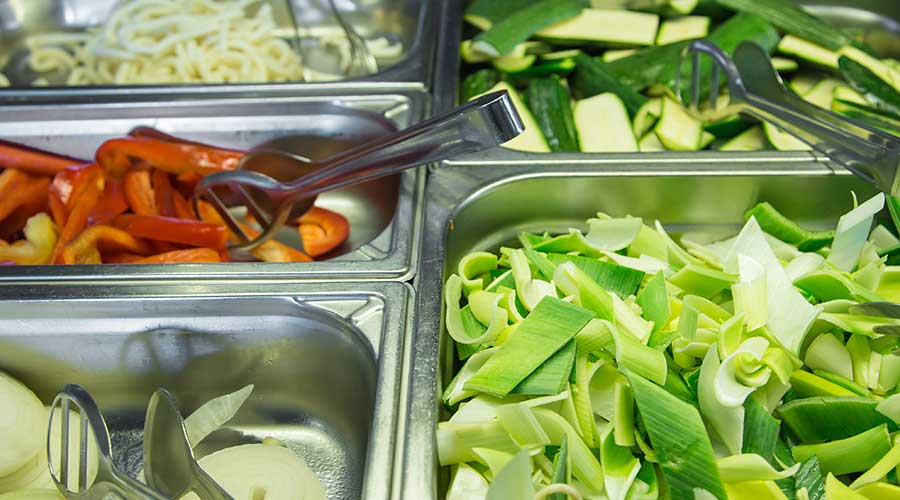
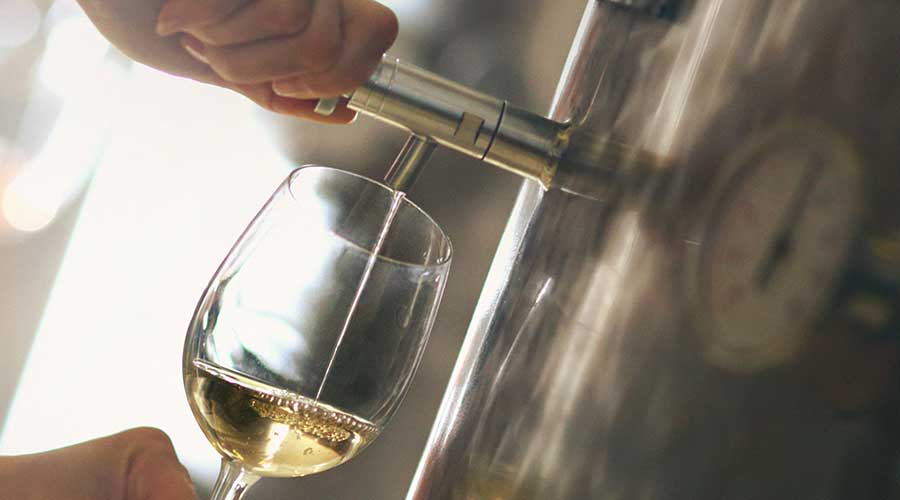
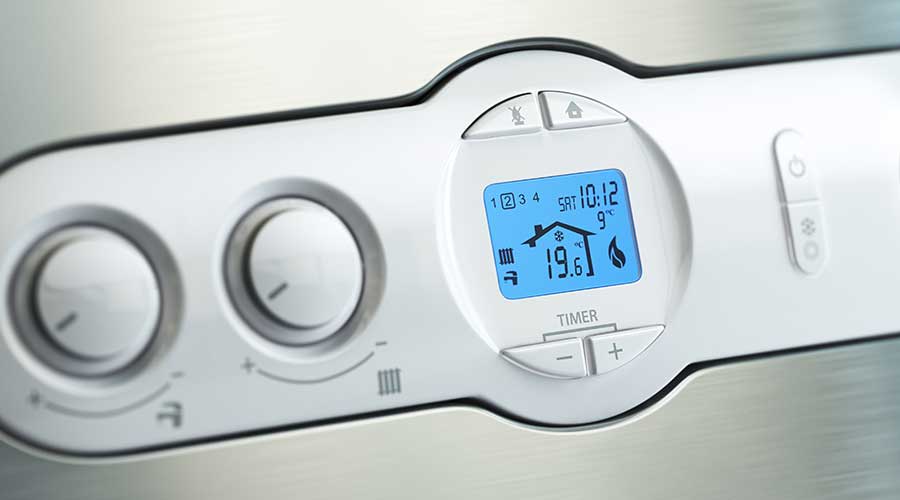
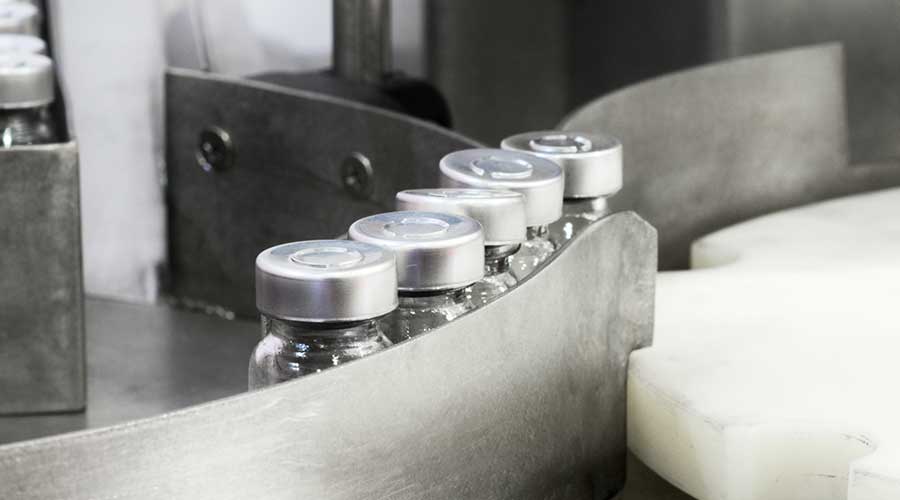
aIsi 304 – X5CrNi18-10
MECHANICAL CHARACTERISTICS | |||||
---|---|---|---|---|---|
Numeral designation |
1.4301 | ||||
thickness [mm] |
shape of product | proof strength Rp [N/mm²] |
Tensile strength Rm [N/mm²] |
Elongation A % min. |
|
Rp 0.2 | Rp 1.0 | ||||
s < 3 | C | 230 | 260 | 540 – 750 | 45 |
H | 210 | 250 | 520 – 720 | ||
P | |||||
s ≥ 3 | C | 230 | 260 | 540 – 750 | 45 |
H | 210 | 250 | 520 – 720 | ||
P |
C = cold-rolled strip
H = hot-rolled strip
P = hot-rolled sheet
CHEMICAL COMPOSITION OF HEAT ANALYSIS (1) | |
---|---|
elements in % | % |
C | ≤ 0.07 |
Mn | ≤ 2.00 |
Si | ≤ 1.00 |
P max. | 0.045 |
S (2) | ≤ 0.015 |
N | ≤ 0.11 |
Cr | 17.00 – 19.50 |
Cu | – |
Mo | – |
Nb | – |
Ni | 8.00 – 10.50 |
Ti | – |
(1) | The product analysis may deviate from the limit values of the heat analysis. |
(2) | For products which are to be machine processed, sulphur content from 0.015 to 0.030% is recommended and allowed. |
aIsi 304L – X2CrNi18-9
MECHANICAL CHARACTERISTICS | |||||
---|---|---|---|---|---|
Numeral designation |
1.4307 | ||||
thickness [mm] |
shape of product |
proof strength |
Tensile strength |
Elongation |
|
Rp 0.2 | Rp 1.0 | ||||
s < 3 | C | 220 | 250 | 520 – 670 | 45 |
H | 200 | 240 | |||
P | 500 – 650 | ||||
s ≥ 3 | C | 220 | 250 | 520 – 670 | 45 |
H | 200 | 240 | |||
P | 500 – 650 |
C = cold-rolled strip
H = hot-rolled strip
P = hot-rolled sheet
CHEMICAL COMPOSITION OF HEAT ANALYSIS (1) | |
---|---|
elements in % | % |
C | ≤ 0.03 |
Mn | ≤ 2.00 |
Si | ≤ 1.00 |
P max. | 0.045 |
S (2) | ≤ 0.015 |
N | ≤ 0.11 |
Cr | 17.50 – 19.50 |
Cu | – |
Mo | – |
Nb | – |
Ni | 8.00 – 10.00 |
Ti | – |
(1) | The product analysis may deviate from the limit values of the heat analysis. |
(2) | For products which are to be machine processed, sulphur content from 0.015 to 0.030% is recommended and allowed. |
aIsi 309 – X15CrNiSi20-12
MECHANICAL CHARACTERISTICS | |||||
---|---|---|---|---|---|
Numeral designation |
1.4828 | ||||
thickness [mm] |
shape of product |
proof strength |
Tensile strength
|
Elongation |
|
Rp 0.2 | Rp 1.0 | ||||
s < 3 | C | ||||
H | |||||
P | |||||
s ≥ 3 | C | ||||
H | |||||
P |
C = cold-rolled strip
H = hot-rolled strip
P = hot-rolled sheet
CHEMICAL COMPOSITION OF HEAT ANALYSIS (1) | |
---|---|
elements in % | % |
C | ≤ 0.20 |
Mn | ≤ 2.00 |
Si | 1.50 – 2.50 |
P max. | 0.045 |
S (2) | ≤ 0.030 |
N | ≤ 0.11 |
Cr | 19.00 – 21.00 |
Cu | – |
Mo | – |
Nb | – |
Ni | 11.00 – 13.00 |
Ti | – |
(1) | The product analysis may deviate from the limit values of the heat analysis. |
(2) | For products which are to be machine processed, sulphur content from 0.015 to 0.030% is recommended and allowed. |
aIsi 310 – X22CrNi25-20
MECHANICAL CHARACTERISTICS | |||||
---|---|---|---|---|---|
Numeral designation |
1.4845 | ||||
thickness [mm] |
shape of product |
proof strength |
Tensile strength
|
Elongation |
|
Rp 0.2 | Rp 1.0 | ||||
s < 3 | C | ||||
H | |||||
P | |||||
s ≥ 3 | C | ||||
H | |||||
P |
C = cold-rolled strip
H = hot-rolled strip
P = hot-rolled sheet
CHEMICAL COMPOSITION OF HEAT ANALYSIS (1) | |
---|---|
elements in % | % |
C | ≤ 0.25 |
Mn | ≤ 2.00 |
Si | ≤ 1.50 |
P max. | 0.045 |
S (2) | ≤ 0.030 |
N | – |
Cr | 24.00 – 26.00 |
Cu | – |
Mo | – |
Nb | – |
Ni | 19.00 – 22.00 |
Ti | – |
(1) | The product analysis may deviate from the limit values of the heat analysis. |
(2) | For products which are to be machine processed, sulphur content from 0.015 to 0.030% is recommended and allowed. |
aIsi 316 – X5CrNiMo17-12
MECHANICAL CHARACTERISTICS | |||||
---|---|---|---|---|---|
Numeral designation |
1.4401 | ||||
thickness [mm] |
shape of product |
proof strength |
Tensile strength |
Elongation |
|
Rp 0.2 | Rp 1.0 | ||||
s < 3 | C | 240 | 270 | 530 – 680 | 40 |
H | 220 | 260 | |||
P | 520 – 670 | 45 | |||
s ≥ 3 | C | 240 | 270 | 530 – 680 | 40 |
H | 220 | 260 | |||
P | 520 – 670 | 45 |
C = cold-rolled strip
H = hot-rolled strip
P = hot-rolled sheet
CHEMICAL COMPOSITION OF HEAT ANALYSIa (1) | |
---|---|
elements in % | % |
C | ≤ 0.07 |
Mn | ≤ 2.00 |
Si | ≤ 1.00 |
P max. | 0.045 |
S (2) | ≤ 0.015 |
N | ≤ 0.11 |
Cr | 16.50 – 18.50 |
Cu | – |
Mo | 2.00 – 2.50 |
Nb | – |
Ni | 10.00 – 13.00 |
Ti | – |
(1) | The product analysis may deviate from the limit values of the heat analysis. |
(2) | For products which are to be machine processed, sulphur content from 0.015 to 0.030% is recommended and allowed. |
aIsi 316L – X2CrNiMo17-12
MECHANICAL CHARACTERISTICS | |||||
---|---|---|---|---|---|
Numeral designation | 1.4404 | ||||
thickness [mm] |
shape of product | proof strength Rp [N/mm²] |
Tensile strength Rm [N/mm²] |
Elongation A % min. |
|
Rp 0.2 | Rp 1.0 | ||||
s < 3 | C | 240 | 270 | 530 – 680 | 40 |
H | 220 | 260 | |||
P | 200 | 520 – 670 | 45 | ||
s ≥ 3 | C | 240 | 270 | 530 – 680 | 40 |
H | 220 | 260 | |||
P | 200 | 520 – 670 | 45 |
C = cold-rolled strip
H = hot-rolled strip
P = hot-rolled sheet
CHEMICAL COMPOSITION OF HEAT ANALYSIS (1) | |
---|---|
elements in % | % |
C | ≤ 0.030 |
Mn | ≤ 2.00 |
Si | ≤ 1.00 |
P max. | 0.045 |
S (2) | ≤ 0.015 |
N | ≤ 0.10 |
Cr | 16.50 – 18.50 |
Cu | – |
Mo | 2.00 – 2.50 |
Nb | – |
Ni | 10.00 – 13.00 |
Ti | – |
(1) | The product analysis may deviate from the limit values of the heat analysis. |
(2) | For products which are to be machine processed, sulphur content from 0.015 to 0.030% is recommended and allowed. |
aIsi 321 – X6CrNiTi18-11
MECHANICAL CHARACTERISTICS | |||||
---|---|---|---|---|---|
Numeral designation | 1.4541 | ||||
thickness [mm] |
shape of product | proof strength Rp [N/mm²] |
Tensile strength Rm [N/mm²] |
Elongation A % min. |
|
Rp 0.2 | Rp 1.0 | ||||
s < 3 | C | 220 | 250 | 520 – 720 | 40 |
H | 200 | 240 | |||
P | 500 – 700 | ||||
s ≥ 3 | C | 220 | 250 | 520 – 720 | 40 |
H | 200 | 240 | |||
P | 500 – 700 |
C = cold-rolled strip
H = hot-rolled strip
P = hot-rolled sheet
CHEMICAL COMPOSITION OF HEAT ANALYSIS (1) | |
---|---|
elements in % | % |
C | ≤ 0.08 |
Mn | ≤ 2.00 |
Si | ≤ 1.00 |
P max. | 0.045 |
S (2) | ≤ 0.015 |
N | – |
Cr | 17.00 – 19.00 |
Cu | – |
Mo | – |
Nb | – |
Ni | 9.00 – 12.00 |
Ti | 5XCI0.70 |
(1) | The product analysis may deviate from the limit values of the heat analysis. |
(2) | For products which are to be machine processed, sulphur content from 0.015 to 0.030% is recommended and allowed. |
Technical characteristics
Technical specifications
Austenitic steels are particular chromium-nickel alloys which feature chromium contents varying from 16 to 26% and nickel contents from 6 to 22% besides generally having a very low carbon content, below 0.1%.
Steels in which part of the nickel is replaced by manganese (about 7%), another austenitizing element, and by nitrogen (0.25% max) may well be mentioned among these steels. They are, of course, less important products with more modest quality characteristics.
Their mechanical characteristics are fairly good and can be increased only by strain hardening by cold plastic deformation (rolling, drawing, etc.) Good resistance to wear and fatigue limit.
Resilience
Austenitic steels are insensitive to brittle fracture at solution annealed condition. As they do not have a pronounced transition temperature, which is an important characteristic of other steels, they are also useful for applications at low (cryogenic) temperatures. Weldability -Stainless steels can be easily welded to other stainless steels and to common carbon steels. To reduce risks of deformation when carrying out joining processes, the physical properties of stainless steel compared to those of carbon steel must be taken into account, such as its greater coefficient of thermal expansion and its lesser thermal conductivity especially in austenitic steels.
TIG welding processes (in an inert atmosphere with a tungsten electrode), plasma arc welding, MIG (inert gas welding with a metal electrode) and resistance welding are all particularly suitable for stainless steel. Resistance butt welding is a rather common technique for joining panels as it does not require work on the backsides and does not create surface alterations. Processability – Excellent processability especially for cold deformations and machine tools (removal of shavin
Dimensional limits
flattened sheets | ||||
---|---|---|---|---|
min / max thickness |
min / max width |
min / max length |
length tolerance | dimensional, shape and mass tolerances |
0.4 – 12.0
|
200 – 2,000
|
400 – 6,000
|
– 0 / + 2
|
according to EN
|
Strips | |||
---|---|---|---|
min / max thickness |
min / max width |
width tolerance | dimensional, shape and mass tolerances |
0.4 – 3.0
|
7.0 – 1,600
|
– 0.2 / + 0.2
|
according to EN
|
Thickness tolerances
Thickness tolerances of flat products are indicated in the two tables below.
The first (I) applies to cold rolled flat products (strips, wide strips and sheets), the second (II) only to continuously hot-rolled products (sheets and strips).
TABLE I – THICKNESS TOLERANCES OF COLD-ROLLED STRIPS, WIDE STRIPS AND SHEETS (UNI EN 10258 – 10259) (1) | ||
---|---|---|
nominal thickness [mm] | cold-rolled sheets, thin sheets, wide strips | |
0.2 < s ≤ 0.4 | +/- 0.05 | +/- 0.03 |
0.4 < s ≤ 0.7 | +/- 0.07 | +/- 0.05 |
0.7 < s ≤ 1 | +/- 0.10 | +/- 0.06 |
1 < s ≤ 1.45 | +/- 0.12 | +/- 0.07 |
1.45 < s ≤ 1.8 | +/- 0.15 | +/- 0.08 |
1.8 < s ≤ 2.1 | +/- 0.17 | +/- 0.09 |
2.1 < s ≤ 2.5 | +/- 0.20 | +/- 0.10 |
2.5 < s ≤ 3 | +/- 0.22 | +/- 0.12 |
3 < s ≤ 3.3 | +/- 0.25 | +/- 0.13 |
3.3 < s ≤ 3.7 | +/- 0.30 | +/- 0.15 |
3.7 < s ≤ 4.25 | +/- 0.35 | +/- 0.18 |
4.25 < s ≤ 5 | +/- 0.35 | +/- 0.20 |
(1) Measurement of the thickness must not be taken at less than 10 mm from the edge
TABLE II – THICKNESS TOLERANCES OF HOT-ROLLED STRIPS, WIDE STRIPS AND SHEETS (UNI EN 10029 – 10051) (1) | ||
---|---|---|
nominal thickness |
tolerance for a nominal width [in mm] | |
L ≤ 1,250 |
1,250 < L ≤ 2,000 | |
s ≤ 5 | + 0.35 / – 0.25 | + 0.50 / – 0.25 |
5 < s ≤ 10 | + 1.20 / – 0.25 | |
10 < s ≤ 19 | + 1.40 / – 0.25 | |
19 < s ≤ 25 | + 1.50 / – 0.25 | |
25 < s ≤ 40 | + 1.80 / – 0.25 | |
s > 40 | to be agreed at the time of ordering |
(1) Measurement of the thickness must not be taken at less than 10 mm from the edge
Surface characteristics
Standard rolled finish
These surface finishes are attained on the steel product directly at the steel mill during rolling and the subsequent treatment cycles.
The various finishes with codes provided for by the AISI standard follow:
Finish no. 0
Only hot-rolled, followed by heat treatment, pickling not provided for
Finish no. 1
It is the typical finish of hot-rolled sheets. It can be attained by hot rolling, followed by annealing, recrystallization or solution annealing according to the martensitic, ferritic and austenitic types, lastly followed by pickling in one or more baths in an acid solution to descale.
It has a matt silver grey appearance and a rough texture.
Finish no. 2D (D = dull, matt)
It is the finish attained by cold rolling with a reduction of thickness by at least 20% of already hot rolled, heat treated and pickled strips with finish no. 1. Cold rolling is followed by a treatment to soften the steel (annealing, recrystallization or solution annealing according to the types of stainless steels) and then pickling.
The surface is not reflective yet, however it is smoother than finish no. 1 because of the cold rolling it has undergone. In addition, thickness is much more constant with more restricted tolerances.
It has a silver grey, matt and smooth appearance.
Finish no. 2B (B = bright)
This finish is attained on strips with a no. 2D finish by a skin pass process with polished rolls. It has a bright silver grey appearance and it is the most widespread finish for cold rolled flat products.
Finish BA (BA = bright annealed)
It is the finish of cold rolled products attained by heat annealing, recrystallization or solution annealing according to the cases, in a controlled atmosphere (basically dissociated ammonia), after rolling and subsequent roughing. Because of the particular thermal treatment, the material does not become oxidized, pickling is therefore not necessary, and it maintains a very bright and reflective look which is typical of cold rolled products. As the formation of oxides is prevented, dechromatization does not take place which is subsequently highlighted by pickling. Any possible alteration of chromium, the most important of the alloy elements, does not take place accordingly, and its surface concentration hence remains equal to the one inside the material.
SURFACE FINISH
Surface quality of stainless steels is extremely important, not only for aesthetic purposes, but, most of all, as regards the intrinsic resistance of the steel in respect to internal corrosion.
We can basically say that resistance to corrosion will be greater when surface smoothness is greater; in other words, the less rough the surface of the stainless steel element is, greater its resistance to corrosion is.
There are rules which codify a certain number of finishes defined “standard”, at least for the most widespread types of products.
They can be divided into three types:
- Standard ground finish
- Scotch Brite finish
- Satin finish
Standard ground finish
These finishes are carried out on stainless steels with the use of abrasives of suitable grain size. Besides the standard finishes provided for by the standard there are also non standard finishes, not classified by standards but implemented for specific purposes.
The descriptions for the various finishes codified by the AISI standard and Gavinox finishes are found below.
Scotch Brite brushing
This kind of surface finish is uni-directional and attained by brushing.
Fibre abrasive rolls are used to make light incisions/etches on the surface of the steel.
Brushing is done with special coarse, medium, fine or extra-fine grain brushes depending on the ultimate outcome required.
Satin finish
This kind of surface finish is uni-directional and attained by grinding with abrasive rolls. These rolls produce incisions/etches on the surface of the steel.
Special abrasive rolls of various grains are used for a satin finish depending on the final desirable outcome.
Duplo
A double finish (duplo) attained by first satin finishing and then brushing to reduce roughness of the surface.
STANDARD SURFACE PROTECTION
- White/white and black/white medium adhesive PVC (approximately 80 microns)
- White/black PVC for CO2 laser cutting and medium/high adhesive fibre (80/100 microns)
- Low adhesive blue PET (60 microns)
- Blue PVC for very deep pressing (60 microns)
Corrosion resistance
AISI 304: it is considered to be corrosion resistant stainless steel in general. It is suitable for not very aggressive outdoor environments.
AISI 304L: it derives from AISI 304 but has a lower carbon content.
AISI 309: it is also known as refractory steel for its capacity of resisting to corrosion at very high temperatures.
AISI 310: it is resistant to high temperatures as AISI 309.
AISI 316: it proves to be especially resistant to pitting corrosion and more resistant than AISI 304 to corrosion under pressure.
It is especially suitable for all outdoor applications such as coastal or industrial areas.
AISI 316L: it derives from AISI 316, has the same corrosion resistance features but lower carbon content.
AISI 321: it is insensitive to intercrystalline corrosion even after welding.
DESIGNATION
These steels must be designated according to the international EN 10088 – 2 standard in the way and order indicated below even though the codes of the American AISI standard are commonly used:
- type of product (strip or sheet)
- number of reference standard
- alphanumeric designation or numeral designation of the steel
- letter referring to the surface finish
Example:
Designation of a strip measuring 200 x 2 of quality X5CrNi18-10 (AISI 301) with cold rolled surface finish, heat treated, pickled and skin-passed.
strip 200 x 2 – EN 10088 – X5CrNi18-10 + 2B or:
strip 200 x 2 – EN 10088 – 1.4301 + 2B