Ferritic stainless steels
Ferritic stainless steel flat rolled products and strips
(EN 10088)
Ferritic stainless steels (ferritic structure) are iron-chromium-carbon alloys in which the chromium values are between 16 and 28%.
The mechanical characteristics of these steels can be increased to a limited extent by subjecting them to the same cold deformation processes which bring about work hardening (drawing, rolling, etc.).
Their wear to resistance is considered to be good.
These stainless steels are the ones that are least suitable for use at low temperatures.
Weldability of conventional ferritic stainless steel is mediocre. Resistance welding (spot welding and roller welding) is the most suitable welding process.
Weldability improves when moving to other structural, stabilized types with low interstitial content.
They are well suited for cold deformation.
Uses
Heat exchanger pipes, distillation towers, car mufflers, cutlery, pots and pans, decorative household objects, washing machine drums, car accessories, cookers.
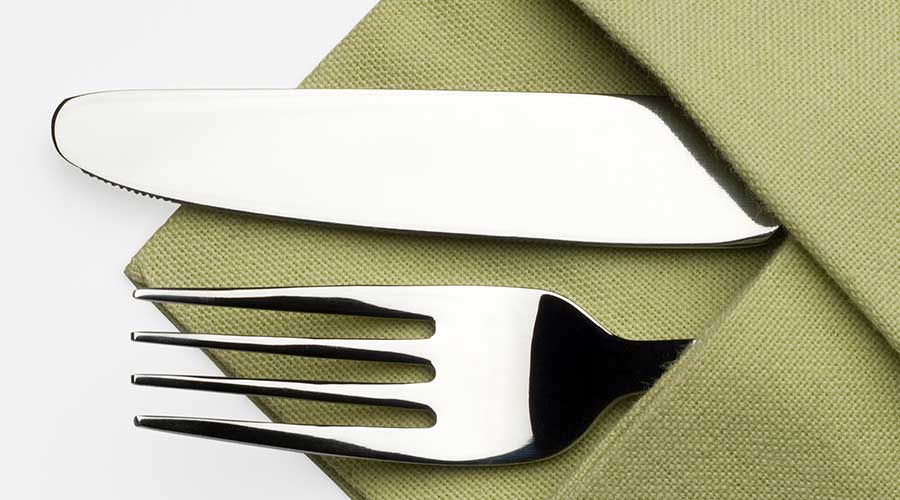
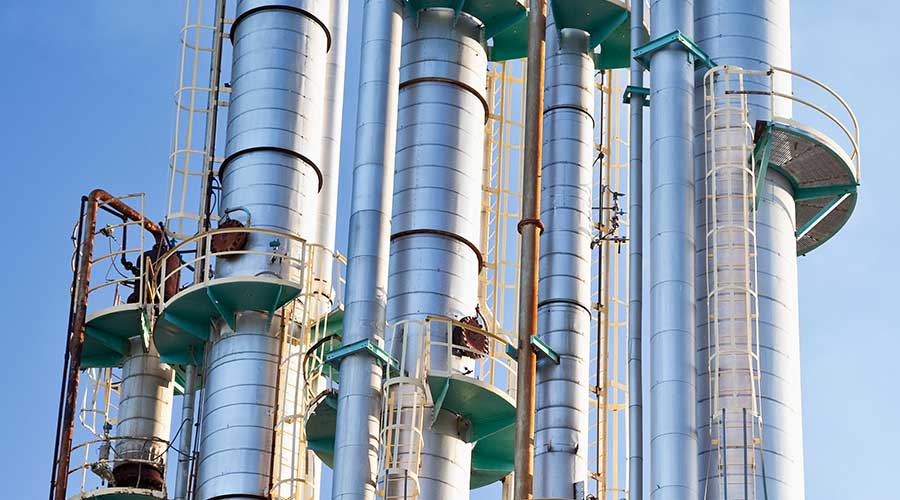
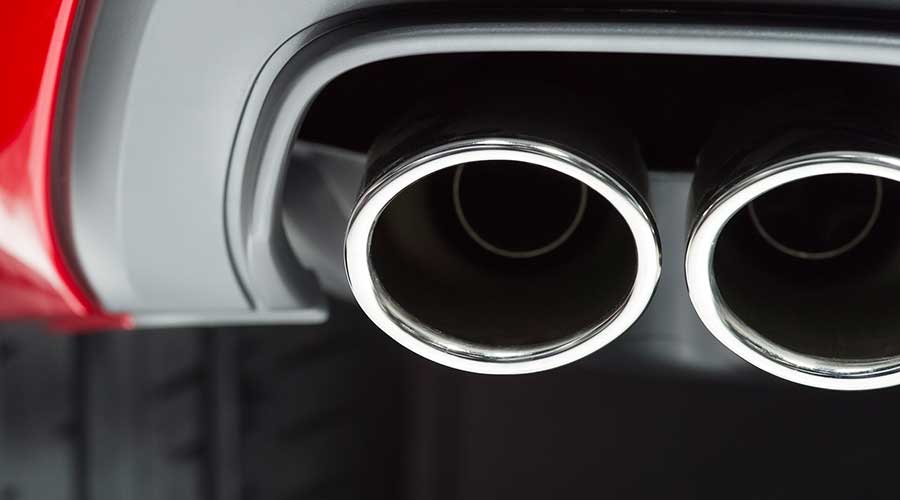
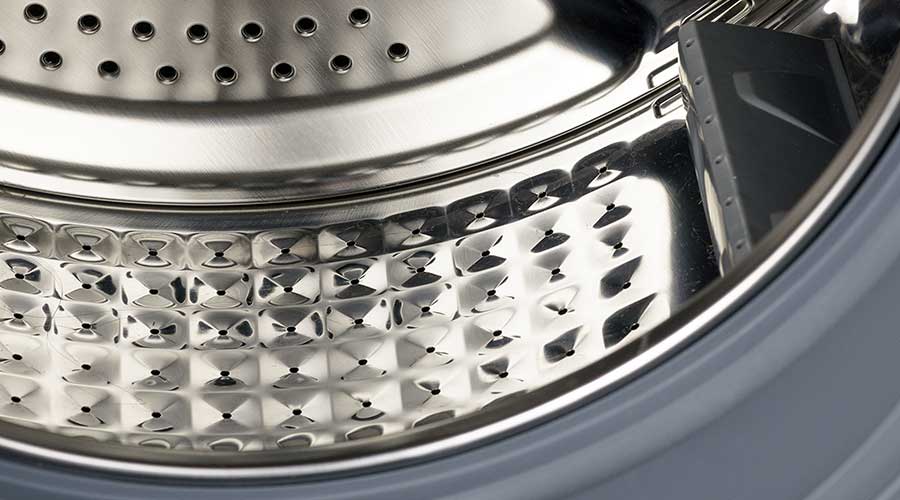
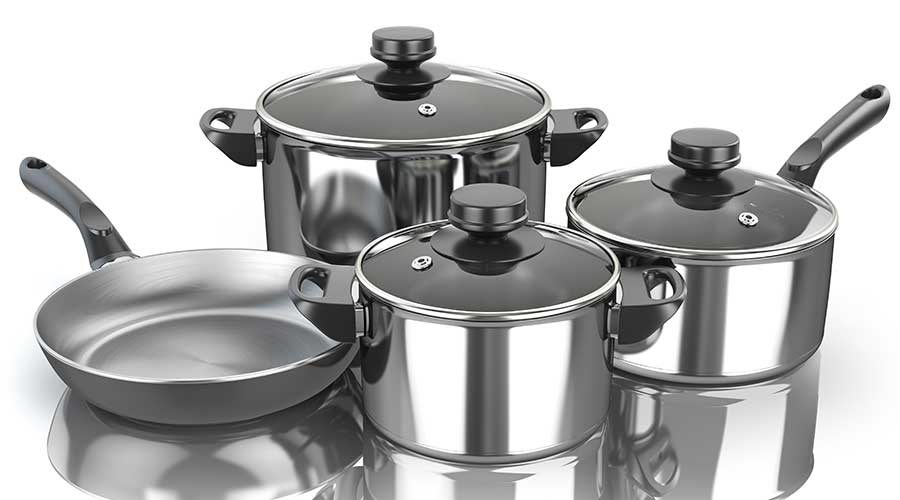
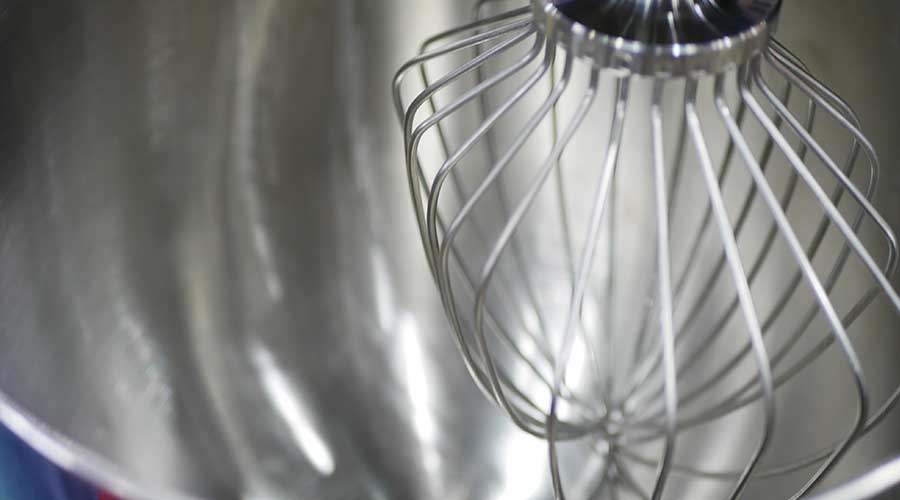
AISI 405 – X6CrAl13
MECHANICAL CHARACTERISTICS | |||||
---|---|---|---|---|---|
Numeral designation | 1.4002 | ||||
thickness [mm] |
shape of product |
proof strength |
Tensile strength |
Elongation |
|
longitudinal | cross | ||||
for all available thicknesses | C | 230 | 250 | 400 – 600 | 17 |
H | 210 | 230 | |||
P |
C = cold-rolled strip
H = hot-rolled strip
P = hot-rolled sheet
CHEMICAL COMPOSITION OF HEAT ANALYSIS (1) | |
---|---|
elements in % | % |
C max. | 0.08 |
Mn max. | 1.00 |
Si max. | 1.00 |
P max. | 0.040 |
S | ≤ 0.015 |
N | – |
Cr | 12.00 – 14.00 |
Cu | – |
Mo | – |
Nb | – |
Ni | |
Ti | – |
others | 0.10 ≤ Al ≤ 0.30 |
(1) The product analysis may deviate from the limit values of the heat analysis.
AISI 409 – X6CrTi12
MECHANICAL CHARACTERISTICS | |||||
---|---|---|---|---|---|
Numeral designation |
1.4512 | ||||
thickness [mm] |
shape of product | proof strength Rp [N/mm²] |
Tensile strength Rm [N/mm²] |
Elongation A % min. |
|
longitudinal | cross | ||||
for all available thicknesses | C | 210 | 220 | 380 – 560 | 25 |
H |
C = cold-rolled strip
H = hot-rolled strip
P = hot-rolled sheet
CHEMICAL COMPOSITION OF HEAT ANALYSIS (1) | |
---|---|
elements in % | % |
C max. | 0.03 |
Mn max. | 1.00 |
Si max. | 1.00 |
P max. | 0.040 |
S | ≤ 0.015 |
N | – |
Cr | 10.50 – 12.50 |
Cu | – |
Mo | – |
Nb | – |
Ni | – |
Ti | – |
others | 6x(C+N)≤ Ti ≤ 0.65 |
(1) The product analysis may deviate from the limit values of the heat analysis.
AISI 430 – X6Cr17
MECHANICAL CHARACTERISTICS | |||||
---|---|---|---|---|---|
Numeral designation |
1.4016 | ||||
thickness [mm] |
shape of product |
proof strength |
Tensile strength Rm [N/mm²] |
Elongation A % min. |
|
longitudinal | cross | ||||
for all available thicknesses | C | 260 | 280 | 450 – 600 | 20 |
H | 240 | 260 | 18 | ||
P | 430 – 630 | 20 |
C = cold-rolled strip
H = hot-rolled strip
P = hot-rolled sheet
CHEMICAL COMPOSITION OF HEAT ANALYSIS (1) | |
---|---|
elements in % | % |
C max. | 0.08 |
Mn max. | 1.00 |
Si max. | 1.00 |
P max. | 0.040 |
S | ≤ 0.015 |
N | – |
Cr | 16.00 – 18.00 |
Cu | – |
Mo | – |
Nb | – |
Ni | – |
Ti | – |
others | – |
(1) The product analysis may deviate from the limit values of the heat analysis.
TECHNICAL CHARACTERISTICS
TECHNICAL SPECIFICATIONS
Ferritic stainless steels are iron-chromium-carbon alloys in which the chromium values are between 16 and 28%.
In addition, depending on their end use, there are other elements such as molybdenum and nickel.
They have a ferritic structure.
The mechanical characteristics of these steels can be increased to a limited extent by subjecting them to the same cold deformation processes which bring about work hardening (drawing, rolling, etc.).
Their wear to resistance is considered to be good.
RESILIENCE
Their toughness at temperatures below ambient shows that these stainless steels are the ones that are least suitable for use at low temperatures.
They have an abrupt drop of resilience as soon as there is a change of the ambient temperature.
WELDABILITY
Weldability of conventional ferritic stainless steel is mediocre. Resistance welding (spot welding and roller welding) is the most suitable welding process.
Weldability improves when moving to other structural, stabilized types with low interstitial content.
PROCESSABILITY
Good processability for cold deformation. Their resulphurised versions guarantee machinability rather well.
DIMENSIONAL LIMITS
FLATTENED SHEETS | ||||
---|---|---|---|---|
min / max thickness |
min / max width |
min / max length |
length tolerance | dimensional, shape and mass tolerances |
0.4 – 12.0
|
200 – 2,000
|
400 – 6,000
|
– 0 / + 2
|
according to EN
|
STRIPS | |||
---|---|---|---|
min / max thickness |
min / max width |
width tolerance | dimensional, shape and mass tolerances |
0.4 – 3.0
|
7.0 – 1,600
|
– 0.2 / + 0.2
|
according to EN
|
Thickness tolerances
Thickness tolerances of flat products are indicated in the two tables below.
The first (I) applies to cold rolled flat products (strips, wide strips and sheets), the second (II) only to continuously hot-rolled products (sheets and strips).
TABLE I – THICKNESS TOLERANCES OF COLD-ROLLED STRIPS, WIDE STRIPS AND SHEETS (UNI EN 10258 – 10259) (1) | ||
---|---|---|
nominal thickness [mm] | cold-rolled sheets, thin sheets, wide strips | |
0.2 < s ≤ 0.4 | +/- 0.05 | +/- 0.03 |
0.4 < s ≤ 0.7 | +/- 0.07 | +/- 0.05 |
0.7 < s ≤ 1 | +/- 0.10 | +/- 0.06 |
1 < s ≤ 1.45 | +/- 0.12 | +/- 0.07 |
1.45 < s ≤ 1.8 | +/- 0.15 | +/- 0.08 |
1.8 < s ≤ 2.1 | +/- 0.17 | +/- 0.09 |
2.1 < s ≤ 2.5 | +/- 0.20 | +/- 0.10 |
2.5 < s ≤ 3 | +/- 0.22 | +/- 0.12 |
3 < s ≤ 3.3 | +/- 0.25 | +/- 0.13 |
3.3 < s ≤ 3.7 | +/- 0.30 | +/- 0.15 |
3.7 < s ≤ 4.25 | +/- 0.35 | +/- 0.18 |
4.25 < s ≤ 5 | +/- 0.35 | +/- 0.20 |
(1) Measurement of the thickness must not be taken at less than 10 mm from the edge
TABLE II – THICKNESS TOLERANCES OF HOT-ROLLED SHEETS, THIN SHEETS, STRIPS AND WIDE STRIPS (UNI EN 10029 – 10051) (1) | ||
---|---|---|
nominal thickness |
tolerance for a nominal width [in mm] | |
L ≤ 1,250 |
1,250 < L ≤ 2,000 | |
s ≤ 5 | + 0.35 / – 0.25 | + 0.50 / – 0.25 |
5 < s ≤ 10 | + 1.20 / – 0.25 | |
10 < s ≤ 19 | + 1.40 / – 0.25 | |
19 < s ≤ 25 | + 1.50 / – 0.25 | |
25 < s ≤ 40 | + 1.80 / – 0.25 | |
s > 40 | to be agreed at the time of ordering |
(1) Measurement of the thickness must not be taken at less than 10 mm from the edge
SURFACE CHARACTERISTICS
Standard rolled finish
These surface finishes are attained on the steel product directly at the steel mill during rolling and the subsequent treatment cycles.
The various finishes with codes provided for by the AISI standard follow.
Finish no. 0
Only hot-rolled, followed by heat treatment.
Finish no. 1
It is the typical finish of hot-rolled sheets. It can be attained by hot rolling, followed by annealing, recrystallization or solution annealing according to the martensitic, ferritic and austenitic types, lastly followed by pickling in one or more baths in an acid solution to descale.
It has a matt silver grey appearance and a rough texture.
Finish no. 2D (D = dull, matt)
It is the finish attained by cold rolling with a reduction of thickness by at least 20% of already hot rolled, heat treated and pickled strips with finish no. 1. Cold rolling is followed by a treatment to soften the steel (annealing, recrystallization or solution annealing according to the types of stainless steels) and then pickling.
The surface is not reflective yet, however it is smoother than finish no. 1 because of the cold rolling it has undergone. In addition, thickness is much more constant with more restricted tolerances.
It has a silver grey, matt and smooth appearance.
Finish no. 2B (B = bright)
This finish is attained on strips with a no. 2D finish by a skin pass process with polished rolls. It has a bright silver grey appearance and it is the most widespread finish for cold rolled flat products.
Finish BA (BA = bright annealed)
It is the finish of cold rolled products attained by heat annealing, recrystallization or solution annealing according to the cases, in a controlled atmosphere (basically dissociated ammonia), after rolling and subsequent roughing. Because of the particular thermal treatment, the material does not become oxidized, pickling is therefore not necessary, and it maintains a very bright and reflective look which is typical of cold rolled products. As the formation of oxides is prevented, dechromatization does not take place which is subsequently highlighted by pickling. Any possible alteration of chromium, the most important of the alloy elements, does not take place accordingly, and its surface concentration hence remains equal to the one inside the material.
SURFACE FINISH
Surface quality of stainless steels is extremely important, not only for aesthetic purposes, but, most of all, as regards the intrinsic resistance of the steel in respect to internal corrosion.
We can basically say that resistance to corrosion will be greater when surface smoothness is greater; in other words, the less rough the surface of the stainless steel element is, greater its resistance to corrosion is.
There are rules which codify a certain number of finishes defined “standard”, at least for the most widespread types of products.
They can be divided into three types:
- Standard ground finish
- Scotch Brite finish
- Anti fingerprint polishing
Standard ground finish
These finishes are carried out on stainless steels with the use of abrasives of suitable grain size. Besides the standard finishes provided for by the standard there are also non standard finishes, not classified by standards but implemented for specific purposes.
The descriptions for the various finishes codified by the AISI standard and Gavinox finishes are found below.
Scotch Brite brushing
This kind of surface finish is uni-directional and attained by brushing.
Fibre abrasive belts are used to make light incisions/etches on the surface of the steel.
Brushing is done with special coarse, medium, fine or extra-fine grit brushes depending on the ultimate outcome required.
Satin finish
This kind of surface finish is uni-directional and attained by grinding with abrasive rolls. These rolls produce incisions/etches on the surface of the steel.
Special abrasive rolls of various grains are used for a satin finish depending on the final desirable outcome.
Duplo
A double finish (duplo) attained by first satin finishing and then brushing to reduce roughness of the surface.
STANDARD SURFACE PROTECTION
- White/white and black/white medium adhesive PVC (approximately 80 microns)
- White/black PVC for CO2 laser cutting and medium/high adhesive fibre (80/100 microns)
- Low adhesive blue PET (60 microns)
- Blue PVC for very deep pressing (60 microns)
CORROSION RESISTANCE
Corrosion resistance of these steels rises with the increase of chromium content in the alloy, especially as regards resistance to heat oxidation (up to 1200°C).
They are essentially immune to cracking due to stress corrosion induced by chlorides, although their resistance to corrosion is not as good as the one of austenitic types.
They cannot be used for cryogenic applications as their microstructure is ferritic (they become fragile at low temperatures).
Their resistance to pitting increases by adding molybdenum, and their resistance under stress is considered good.
Good resistance to corrosion due to weather conditions especially after high-luster polishing.
AISI 409: it is also called “muffler grade” (the type for mufflers) and often used for catalytic exhausts.
ASI 430: it has good corrosion resistance characteristics both at ambient temperature, and at higher temperatures (not greater than 700°C however) and is heat resistant to dry sulphurous gases.
It has acceptable resistance to pitting and is good under stress.
DESIGNATION
These steels must be designated according to the international EN 10088 – 2 standard in the way and order indicated below even though the codes of the American AISI standard are commonly used:
- type of product (strip or sheet)
- number of reference standard
- alphanumeric designation or numeral designation of the steel
- letter referring to the surface finish
Example:
Designation of a strip measuring 200 x 2 of quality X5CrNi18-10 (AISI 301) with cold rolled surface finish, heat treated, pickled and skin-passed.
strip 200 x 2 – EN 10088 – X5CrNi18-10 + 2B or:
strip 200 x 2 – EN 10088 – 1.4301 + 2B